Brake rubbing: why it happens
A rubbing brake is not only annoying, it also reduces safety and increases wear. We shed light on the causes and solutions.
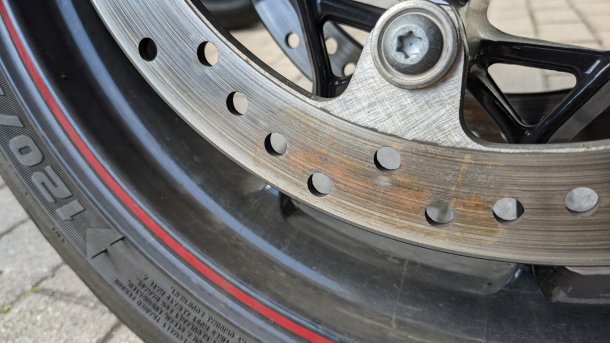
(Bild: Clemens Gleich)
- Clemens Gleich
In my now quite long time as a vehicle tester, I have experienced a lot of rubbing brakes on test bikes – for a wide variety of reasons. As I'm currently dealing with a persistent brake rubbing problem on my own motorcycle, I'll also report on solutions from the field. Brake rubbing always has the same effect: the braking effect of the pads changes over the course of the disk, which leads to noticeable vibrations in the handlebars/steering wheel and in the rest of the vehicle. The causes of this vary considerably.
Top layer
The most common cause in my case and probably in general is in the top layer of the disk. A different coefficient of friction can form there if, for example, the pads on the windshield become very rusty (depending on the material pairing of windshield and pads). In cars, this used to happen more frequently with organic brake pads when braking: the pads get hot, you come to a standstill when braking (often unintentionally due to traffic flow) and the pads stick. The cause of rubbing may then have already been established. However, it can also be caused by dry dirt or a complex combination of several factors. It is typical for problems on the top layer that the rubbing increases (or only becomes noticeable at all) when the brake reaches operating temperature ("hot rubbing").
In such cases, you would think: "Well, it'll go away" because this is usually the case with normal flash rust. However, the rubbed spots locally change the material transition between pad and disk, so that the different coefficient of friction is permanently perpetuated. There is only one remedy here: the top layer must be removed. I have often read that people grind out these spots with sandpaper. The jumps in the friction coefficient are usually clearly recognizable by the imprint of the coating. I have never been able to grind them off in this way. You also have to be a little careful not to remove so much material that you lay the foundation for later rubbing due to material inequality.
(Bild: Clemens Gleich)
In my case, the only thing that helped was to turn off the brake disk (car) or grind it in parallel again (motorcycle). For this to be worthwhile compared to new discs, the brake discs have to be correspondingly expensive. With 0815 everyday car discs, new discs are usually cheaper. Turning costs 40 to 90 Euro per disk. For motorcycles, parallel grinding costs 100 to 200 Euro per disk, depending on the supplier. New discs cost 160 to 270 Euro per disc, so the situation here is similar to that for cars: it is more worthwhile for the expensive sports brake systems. The prerequisite is, of course, a sufficient minimum thickness that is still correct after the material has been removed. Carbon fiber ceramic brake discs (CMC) are immune to most such surface causes.
Lateral run-out
Many KTM customers are familiar with a more perfidious variant: Every new brake disc rubs again and again after a few thousand kilometers, even when cold ("cold rubbing"). The reason for this is a slight lateral run-out of the wheel suspension, which often occurs at the KTM factory in Mattighofen when the rims are re-clamped for milling the wheel bearing mounts. It is not noticeable during normal riding (unlike severe lateral run out), but it causes the disk to wear unevenly. After a certain amount of time, it becomes unevenly thick and rubs.
You could turn off or parallel grind such a disk if the uneven wear is not already too advanced. In the case of such heavy wear, grinding/turning is rarely worthwhile considering the reduced residual thickness. It is best to turn your wheels once along the feeler gauge and measure the lateral run-out at the latest after the first, suspiciously early brake disk replacement. This doesn't cost much, even if you buy your own tools, and the data is very valuable, even if only as an exclusion criterion.
(Bild: Clemens Gleich)
In addition to a new or reground rotor, the remedy here is to straighten the brake rotor track because without this, the new rotor will suffer the same fate. The simplest causes are very unevenly tightened bolts, which pull the brake disk out of the ideal plane, or contamination during installation. Following the workshop manual (i.e. usually crosswise), tightening to the correct tightening torques with threadlocker and torque wrench and keeping all parts meticulously clean can help.
It becomes more expensive if the bike runs crooked overall (the KTM error described above). Here, and I say this from painful experience, you must be careful that the workshop does not simply re-torque the brake disk mount (which almost every workshop can do). If they do this, they clamp the wheel over the crooked axle milling and simply re-mill the crooked plane, which can't help. No, the wheel bearings have to be removed, and the mounts milled straight again. Almost no workshop can do this, so the wheel often has to be sent to these specialist workshops. In my case, this cost 200 euros for a motorcycle rim, which I liked better than 470 euros for a new rim.
Uneven wear
There is another cause that is more difficult to diagnose than lateral runout, which is easy to measure with a dial gauge: uneven disk material thickness without lateral run out. I have read that this can already happen when braking in incorrectly, i.e. when no reliable material transfer has yet been able to form. I always brake in new disks. The best place to do this is, of course, a closed-off stretch of road or a large square - something where you don't have to stop unplanned with a hot brake system. In my experience, the quickest way to do this is on the racetrack, because there is a lot of different but reliable braking without stopping. I carefully brake the first carry-over layer on the track and then drive my normal turns at a steadily increasing speed.
(Bild: Clemens Gleich)
Another cause may be poorly moving brake pistons (and in the case of floating callipers: pins or hinges). Here, minimal manufacturing tolerances, which would otherwise be unproblematic, can ultimately lead to rubbing from uneven wear that can hardly be remedied. With the pads removed, the pistons should come out evenly when the brakes are applied (carefully!). For better observation, block the piston on the other side of the vehicle. Clean the pistons, especially on motorcycles, before pressing them in, DO NOT squeeze them back in with dirt.